Three ships cleverly arranged in the dock, craftsmanship creates a new record - the company refreshes the best performance in foreign ship docking and repair operations
Release time:
2025-04-12
Source:
In early April, the company meticulously planned and simultaneously arranged for a Panamax bulk carrier, "Ruian Bay", and two Handysize bulk carriers, "African Canary" and "Dayuan Glory", to dock in No. 1 dry dock. Through scientific planning and efficient execution, the company significantly improved dry dock efficiency and successfully completed its production plan targets.
Since the beginning of the year, the company's ship repair and modification business has ushered in a production peak, with a promising outlook. This has also led to increasing pressure on the docking periods of the two dry docks, one of 30 ten thousand 20 ten thousand tons 4 At the beginning of the month, for the first time, the company carefully planned and 1# In the dry dock, simultaneously arranged a Panama-type bulk carrier "RYAN BAY" and two HANDY type bulk carriers "AFRICAN ROLLER" and "DAIWAN GLORY" for docking operations. Through scientific planning and efficient execution, the docking efficiency was significantly improved, and the predetermined production plan targets were successfully completed.
Scientific Planning, Precise Cooperation, and Reaching New Heights in Production Efficiency
Faced with 1# dry dock (length 355 meters, width 78 meters) space limitations and extremely high operational precision requirements, the company knew that it must rely on scientific planning and efficient execution to improve docking efficiency. Therefore, with scientific planning as the guide, the Production Department took the lead, in conjunction with the Technology Department, the Dry Dock Service Workshop, and other relevant departments, holding several special planning meetings. Each department worked together precisely, making comprehensive and detailed plans for the production process. By optimizing ship arrangement, refining the shifting order, precisely calculating the placement of the dry dock blocks and the docking sequence, and repeatedly rehearsing the docking and undocking connection plan, a set of efficient and safe operation procedures was finally formed, effectively reducing unnecessary waiting time and operational errors, and raising production efficiency to a new level.
Precise Deployment, Technology Support, and Enhanced Docking Efficiency Through Collaboration
On the early morning April 5th, in the gentle spring rain, employees from the Production Department, Dry Dock Service Workshop, and Tugboat Department, etc., with full work enthusiasm, launched the ship docking campaign. After continuous 7.5 hours of collaborative efforts, all the standard dry dock blocks were successfully placed on the same day at 14:20 minutes, laying a solid foundation for subsequent operations.
In the crucial docking phase, under the precise command of three excellent pilots from the Production Department, relying on their rich experience and superb skills, the three ships overcame difficulties such as low visibility and complex currents, and at 18:30 minutes, they successfully entered the dock in a safe, stable, and orderly manner, fully demonstrating the company's first-class level of pilotage operations. During the entire operation, the company's multiple gantry cranes, tractors, winches, and other production equipment worked efficiently together, and personnel from various relevant departments cooperated tacitly. After nearly 24 hours of uninterrupted operation, the floating positioning and block setting tasks for the three ships were successfully completed by the next morning at 7:51 minutes. Compared with similar-scale ship docking operations in the past, the ship docking time in this operation was significantly shortened, and the docking period was efficiently utilized, setting a new benchmark for the company's similar operations.
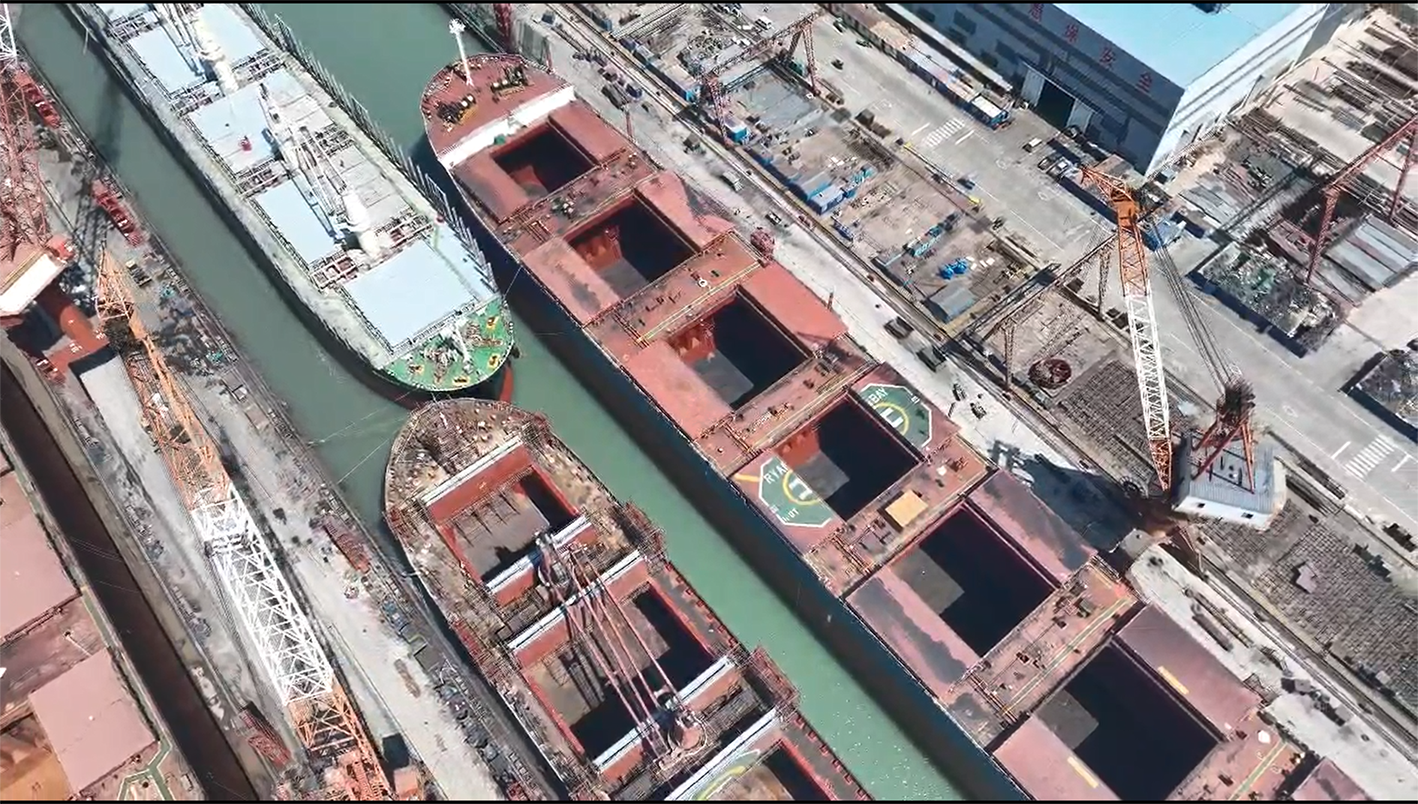
Extreme Operation, Millimeter-Level Precision, Demonstrating Core Strength
The difficulty of this operation also lies in its extremely high precision requirements. The minimum distance between the hulls of the three ships is only 400 millimeters; the average distance between the ships and the dock walls is 1100 millimeters, and the minimum distance is only 370 millimeters; the stern is only 1200 millimeters from the dock gate. Such highly difficult extreme operations fully demonstrate the company's core strength in the ship repair field.
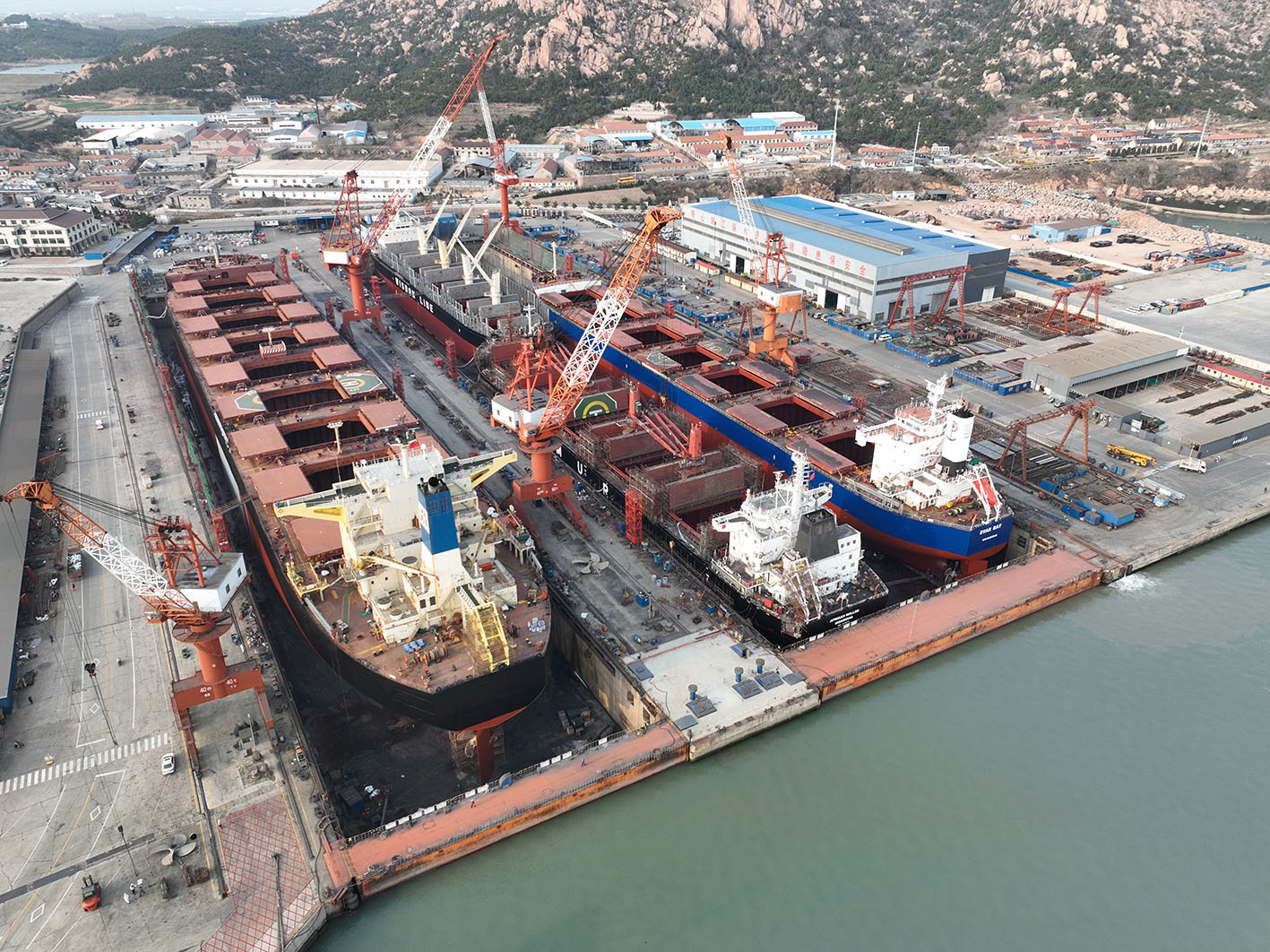
Tribute to the Striver, Perseverance in the Wind and Rain, the Light in the Ordinary
From dawn to late night, from gentle spring rain to bright lights, at the company's dry dock operation site everywhere you could see figures working selflessly. They were drenched but remained focused, they worked continuously without complaint. Under the hard work of all participants day and night, the three ships safely left the dock as planned on the morning of 4 Month 10 day. It is the dedication and responsibility of these ordinary workers that have forged the company's team spirit of "dare to fight hard battles and be able to win hard battles."
The successful completion of the simultaneous docking and repair of the three ships not only created a new record in the company's history of foreign ship docking and repair production, but also demonstrated the company's professional strength and service quality in the ship repair field. In the future, the company will continue to be customer-oriented, driven by technological innovation, continuously improve efficiency, break through limits, and provide strong support for the company's high-quality development.
Other News
On April 9, 2025, CUD (Weihai) Shipyard Co., LTD. and CSSC Chengxi Huarxin Special Coating (Wuxi) Co., LTD., a subsidiary of China Shipbuilding Group Corporation, officially signed a strategic cooperation agreement in Shi Dao, Weihai.